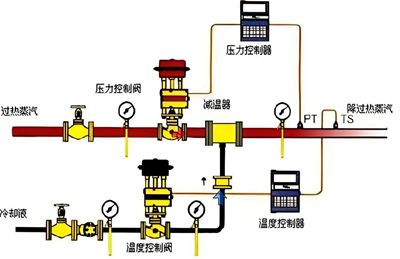
What are the common faults and solutions of pneumatic solenoid valves?
1、 Leakage problem of pneumatic control valve
Leakage of pneumatic valves is one of the more common faults.
How to replace the aging seal that causes leakage?
After long-term use, seals will gradually age and lose their elasticity due to factors such as gas erosion, temperature changes, and mechanical wear, leading to leakage. When replacing the seal, the first step is to turn off the gas source of the air control valve and remove it from the system. Then, carefully disassemble the pneumatic valve and locate the aging seal. When choosing a new seal, it is important to ensure that its material is the same as or has better corrosion and wear resistance than the original seal, and that its size matches perfectly. When installing new seals, pay attention to cleaning the installation area to avoid impurities affecting the sealing effect. At the same time, install them in the correct order and method to ensure that the seals are installed firmly and without distortion.
2. Key points for repairing or replacing valve bodies caused by leakage due to valve body damage.
Valve body damage may be caused by external impact, corrosion, or manufacturing defects. For minor valve body damage, repair methods such as welding and filling can be used. But before repairing, it is necessary to thoroughly clean and inspect the valve body to determine the extent and location of the damage. If the valve body is severely damaged and cannot be repaired, a new valve body needs to be replaced. When replacing the valve body, it is necessary to choose a product with the same model and reliable quality as the original valve body, and ensure that the connection between the valve body and the pipeline is tight and leak free during installation.
2、 Abnormal operation of pneumatic control valve
Abnormal operation of the pneumatic valve can affect the normal operation of the entire system.
How to solve the problem of insufficient air source pressure affecting operation?
Insufficient gas source pressure is one of the common reasons for abnormal operation of pneumatic control valves. This may be caused by faults in the gas supply system, pipeline leaks, or excessive use of gas equipment. To solve the air source problem, the first step is to check the air supply system to ensure the normal operation of the air source equipment, such as whether the pressure setting of the air compressor is correct and whether the filter is clogged. Secondly, it is necessary to inspect the gas pipeline, locate and repair the leakage points. If the pressure is insufficient due to excessive use of gas equipment, you can consider increasing the gas supply or optimizing the usage time of the gas equipment.
2. Precautions for replacing worn parts due to abnormal movement caused by internal component wear.
The internal components of the pneumatic valve, such as the valve core and stem, may experience wear and tear after long-term use, leading to abnormal operation. When replacing worn parts, it is necessary to accurately identify the worn parts and select new parts with qualified quality and dimensional accuracy that meet the requirements. When disassembling old parts, pay attention to recording the installation position and sequence of the parts to avoid errors during installation. When installing new parts, apply an appropriate amount of lubricating oil to ensure smooth movement of the parts, and tighten the screws according to the specified torque to prevent loosening of the parts.
3、 Air control valve blockage fault
Blockage of the gas control valve can cause the gas to flow abnormally.
1. An effective method for removing impurities from blocked channels.
Impurities may enter the interior of the pneumatic valve and block the passage. When cleaning impurities, the first step is to remove the air control valve, and then use compressed air to blow away large particles of impurities in the channel. For smaller impurities, cleaning agents can be used for soaking and rinsing. During the cleaning process, small tools such as toothpicks, needles, etc. can be used to carefully clean the blocked area, but care should be taken to avoid scratching the inner wall of the channel. After cleaning, dry the channel with clean compressed air to ensure there are no residual cleaning agents or moisture.
2. Measures to prevent blockage caused by oil contamination.
Oil contamination is also one of the common causes of air control valve blockage. To prevent oil contamination, a filter needs to be installed at the inlet of the air source to filter out oil mist and moisture in the air. At the same time, it is necessary to regularly inspect and replace the filter to ensure its filtering effectiveness. In addition, when maintaining and repairing the air control valve, it is necessary to avoid using tools and materials with oil stains to prevent oil from entering the interior of the air control valve.
4、 Control failure of pneumatic valve
Control failure will prevent the pneumatic valve from working as expected.
1. Electrical control system malfunction, troubleshooting and repairing electrical problems.
Electrical control system faults may include short circuits, open circuits, poor contacts, and controller failures. When troubleshooting, electrical testing tools such as multimeters should be used to check the continuity and voltage of the circuit. For areas with poor contact, it is necessary to reconnect or replace the connector. If it is a controller malfunction, corresponding maintenance or replacement should be carried out according to the type and symptoms of the controller.
2. Techniques for repairing or replacing mechanical transmission components that have malfunctioned.
Malfunctions in mechanical transmission components such as connecting rods and gears can lead to the failure of pneumatic valve control. When repairing or replacing these components, carefully observe the fault phenomenon and identify the faulty component. Then, disassemble the faulty component and inspect for wear, deformation, or damage. For worn components, they can be repaired or replaced; For severely deformed or damaged components, they must be replaced with new ones. When installing new or repaired components, pay attention to adjusting their position and clearance to ensure smooth transmission.
5、 Excessive noise from the pneumatic valve
Excessive noise can affect the working environment and the normal operation of equipment.
1. Unstable airflow generates noise, and methods to stabilize the airflow.
Unstable airflow may be caused by fluctuations in gas source pressure, inappropriate gas path diameter, or internal structural issues of the air control valve. To stabilize the airflow, a pressure regulator valve can be installed to adjust the air source pressure and keep it stable. At the same time, it is necessary to choose the diameter of the gas path reasonably to avoid too small a diameter causing excessive airflow velocity. For internal structural issues of pneumatic valves, such as poor fit between the valve core and seat, grinding or adjustment can be carried out to improve the stability of the airflow.
2. The operation steps for tightening parts due to noise caused by loose parts.
Loose parts can cause vibration and noise during gas flow. When tightening parts, first identify the loose parts, and then use appropriate tools to tighten screws or nuts according to the specified torque. During the fastening process, be careful not to apply excessive force to avoid damaging the parts.
6、 Maintenance and prevention of pneumatic valves
Proper maintenance and prevention work can extend the service life of pneumatic valves and reduce the occurrence of malfunctions.
The importance and cycle of regular maintenance.
Regular maintenance is crucial for the normal operation of pneumatic valves. It is recommended to conduct a comprehensive inspection and maintenance of the pneumatic valve at regular intervals, with the specific cycle determined by the usage environment and work intensity, generally ranging from 3 months to 6 months. During maintenance, it is necessary to check the condition of the seals, clean impurities and oil stains, inspect the wear of parts, and promptly handle and replace them.
2. Precautions for daily use to extend the lifespan of pneumatic valves.
In daily use, it is important to avoid overloading and overspeed operations to prevent damage to the pneumatic valve. Keep the air source clean and dry to prevent impurities and moisture from entering the air control valve. In addition, when installing and disassembling pneumatic valves, handle them gently to avoid collisions and damage.
In short, understanding the common faults and solutions of pneumatic valves, and carrying out maintenance and prevention work can effectively improve the performance and service life of pneumatic valves, ensuring the normal operation of the system.
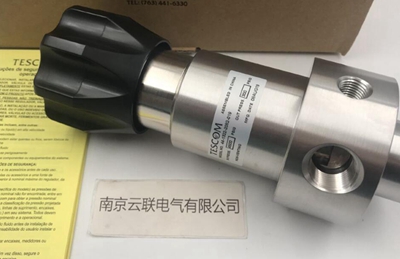